HOW FREE CAN WE BE?
Without being bound by convention, and free to explore your musical potential. Free to experience the highest state-of-the-art technology. On our side - free to express the highest standards of craftsmanship. And for all of us together - to be free to give our best.
We meticulously pay attention to every detail of our instruments allow each player to express themselves as freely as possible.
For the listener, we want to deliver an unprecedented musical experience.
We will continue our pursuit, continue to do research, and develop instruments that offer musical freedom to those that enjoy both playing and listening.
We hope that our instruments will accompany on your musical journey, throughout your lifetime!
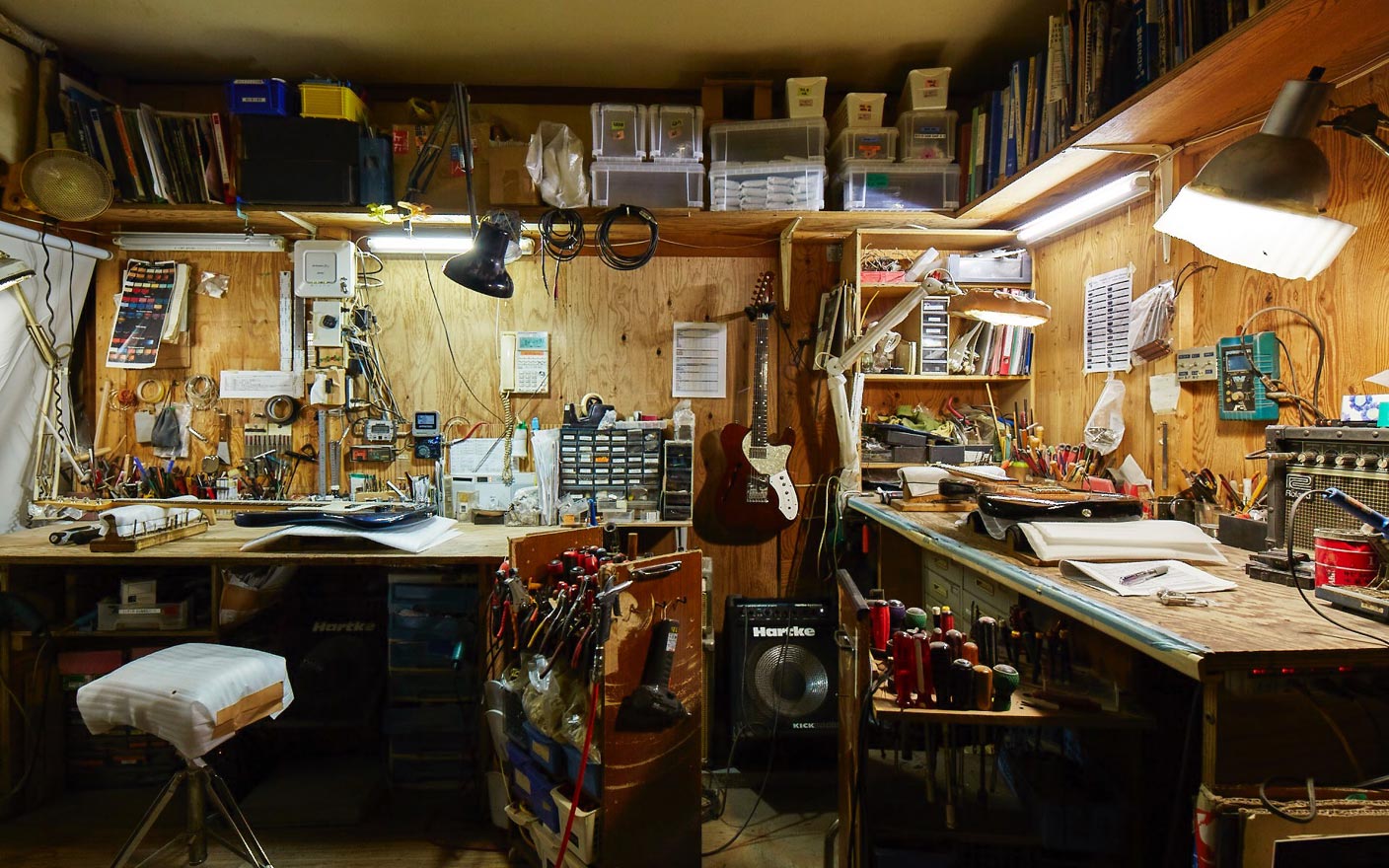
CRAFTSMANSHIP
Like master craftsmen of old, we at FCGR are striving to build instruments that will be playable for over a 100 years.
Such a promise requires utmost commitment to quality in production, and excludes any compromise.
Our instruments combine state-of-the-art technological solutions with traditional luthiery skills to achieve unprecedented quality.
You, as the player of our instruments, deserve nothing less!
Whether you are a touring professional, or a living-room musician playing for your own pleasure, our commitment to you is the same. To help you freely express yourself through music, we will ceaselessly work to maintain and improve our work.
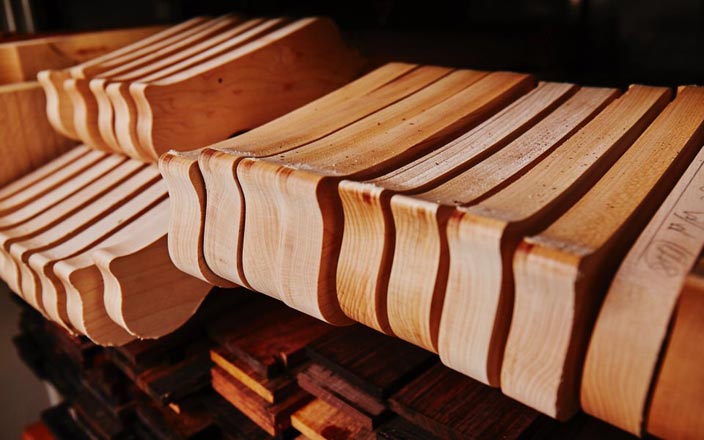
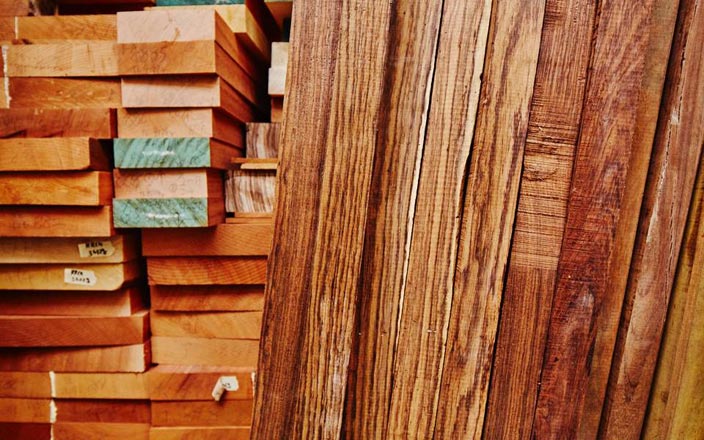
WOOD
Our guitars are produced in central Tokyo, because this is one of the most variable environments in Japan. Temperature and humidity are highly variable, and use of aircons is common. It is our mission to produce instruments that can withstand such varying circumstances, and remain in top playing condition. We source our woods from various parts of the world, through a careful selection process. After thorough inspection, the wood is put in our constant-humidity warehouse to stabilize it, for at least a year.
Only after we are fully satisfied that the wood has reached full stability do we start shaping it into an instrument.
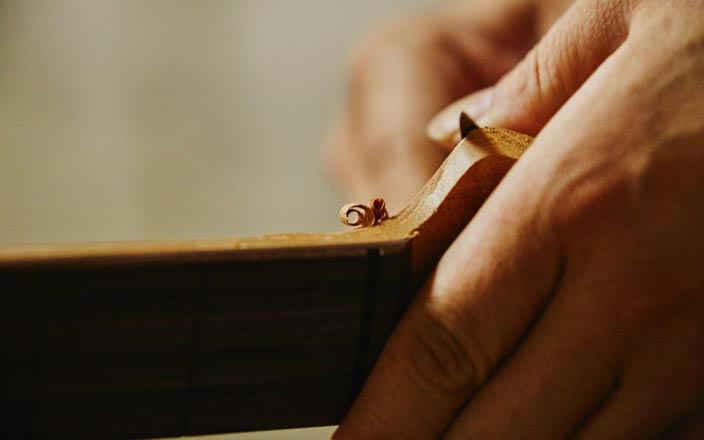
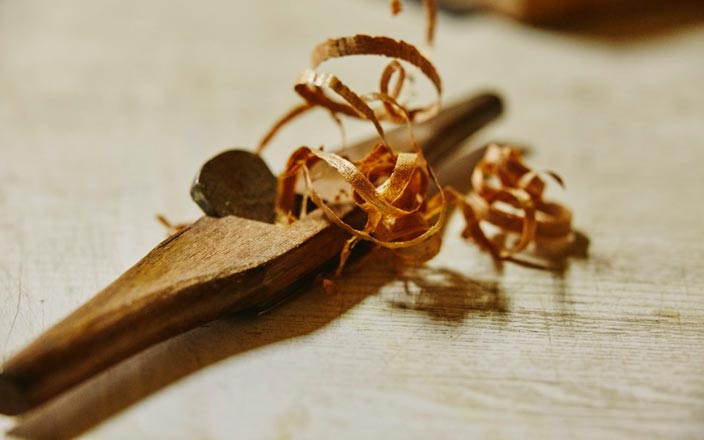
NECK
Of all the components of a guitar, neck is the one where stability is most important. To maintain best playability, even slight misalignments cannot occur.
To produce necks which remain solid throughout the instrument's lifetime, we follow a three-step process.
At each stage, we let the wood rest for at least 2-3 weeks in the warehouse, re-cutting the blank and checking for warpage at each stage. When the wood has reached full stability, we begin shaping the neck.
Each neck is hand shaped by our skilled craftsmen, and the frets are driven in with utmost precision.
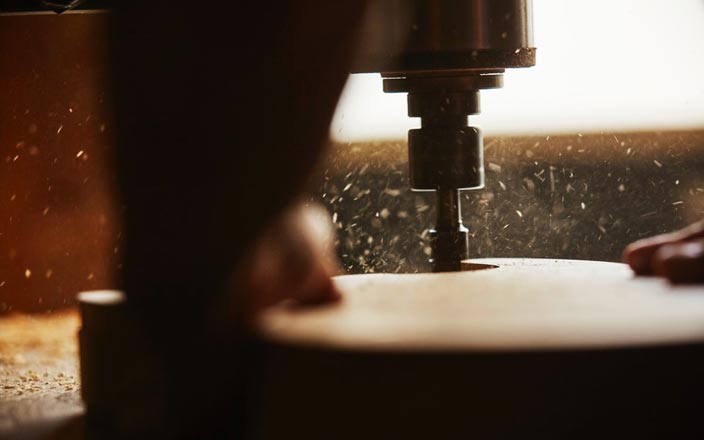
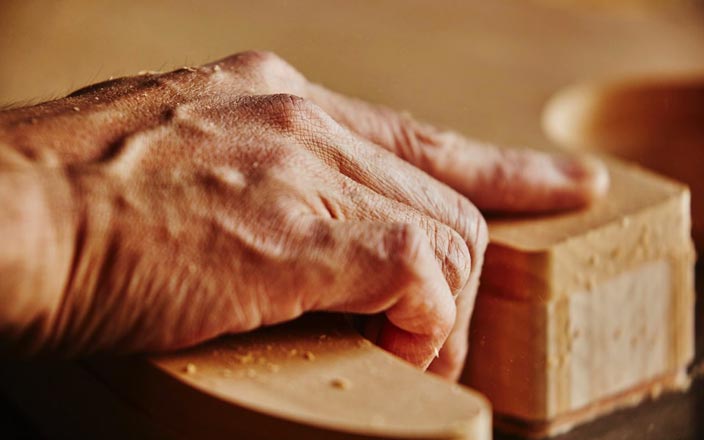
BODY
Like our necks, also our body wood blanks undergo a stabilization process before shaping.
In addition, we check each blank indoividually to match its sonic characteristics with the neck, and ensure that all glue joints are secure. Beyond sounding great, we ensure that the wood grain or other patterns align beautifully to create a guitar that plays well and looks fantastic.
At each step, the instrument is treated as an individual project, and not a mass-produced item.
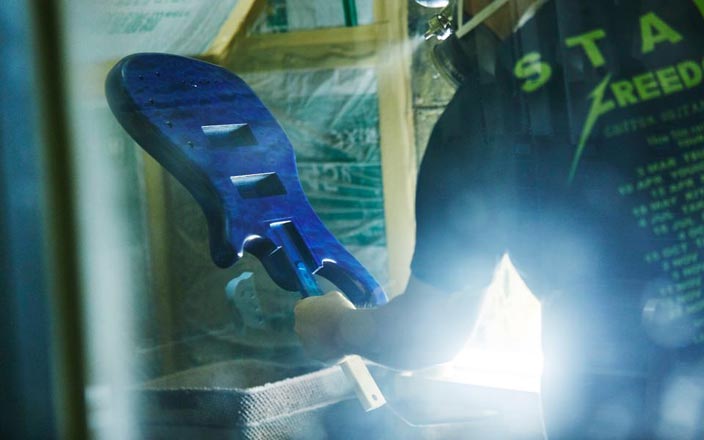
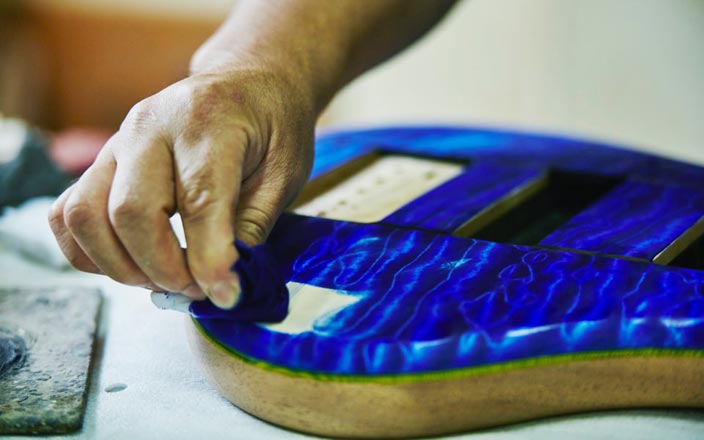
COLOR
There is a story behind each of our original colours - and we continue to develop new ones all the time!
Since the thickness, and type, of paint and lacquer used influences the resonance of the instrument, we can use our years of experience to produce a finish that brings out the character of your individual instrument.
We welcome you to inspect our colour chart, and visit our showroom if possible to see our finishes in person. And if there are colours that you would like on your instrument and cannot see on our page - please let us know, we'll do our best meet your request.

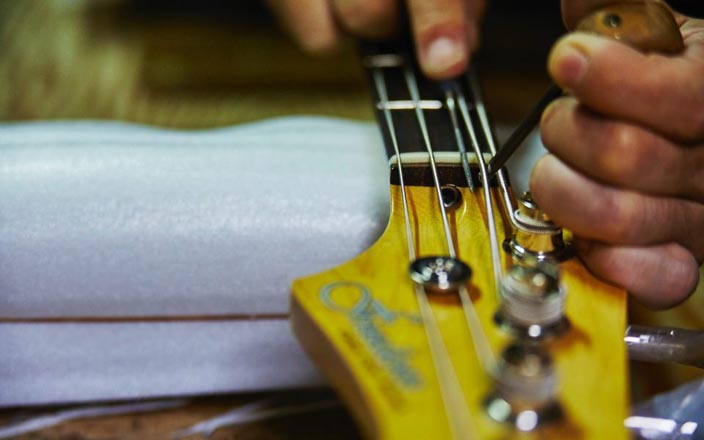
FRETWORK & SET UP
Our stainless-steel fret wire has been specially developed by F.C.G.R. to be completely rust-proof, and eliminate the necessity for maintenance for the lifetime of the instrument. Additionally, our stainless steel produces a warmer sound, eliminating the excessive brightness often associated with typical stainless steel frets.
Often guitars and basses are strung up for the first time after the fretwork and set-up have been completed. At F.C.G.R. after the necks are painted, we assemble the full instrument and tension up their strings for a few weeks - this allows the neck to settle into its final stable shape.
Using a specially designed rig, we then adjust the frets with the neck in its final playing position, with the same curvature as when strings are present. Through this process we can achieve the highest standard for our fretwork, which can not be achieved in mass-produced instruments.